Application highlights
Oil separation is a very commonly used technology with an endless range of products and suppliers. Our products and solutions are developed for those applications where the focus is on what the equipment can do for the process and product quality, not on the separated oil.
Oil separation is not about separating pure clean oil from fresh water, it is about removing polllutants from an aqueous medium. Oil is not ‘oil’ but a mixture of mineral oils, fat, chemicals, water and dirt. And water is not fresh water but a mixture of water, dirt, oils and, with cleaners and emulsions, all sorts of chemicals. Separation theories and laboratory results are not representative for reality and a good understanding of the applications is an absolute necessity.
The Suparator® technology has been approved over the years to be able to handle the pollution in industrial applications and function regardless of other pollutants, besides oil.
Application highlights
Coolant oil separation
Coolant and emulsions often are polluted with lubricating and hydraulic oils. Since the emulsion itself is already a mixture of oil, water and chemicals, this ‘strange’ oil or ‘tramp’ oil can have significant negative effects on the production process which depends on the quality of the emulsion.
The interaction between the tramp oil and the emulsion can have several negative effects on the quality and lifetime of the emulsion. A very common problem is bacteria growth in the coolant, due to the presence of tramp oil, especially in stagnant situations.
In the application where the picture to the left was taken, another problem played a significant role.. The tramp oil cause problems with the automatic changing of tools because they were sticking in the fitting, due to the oil.
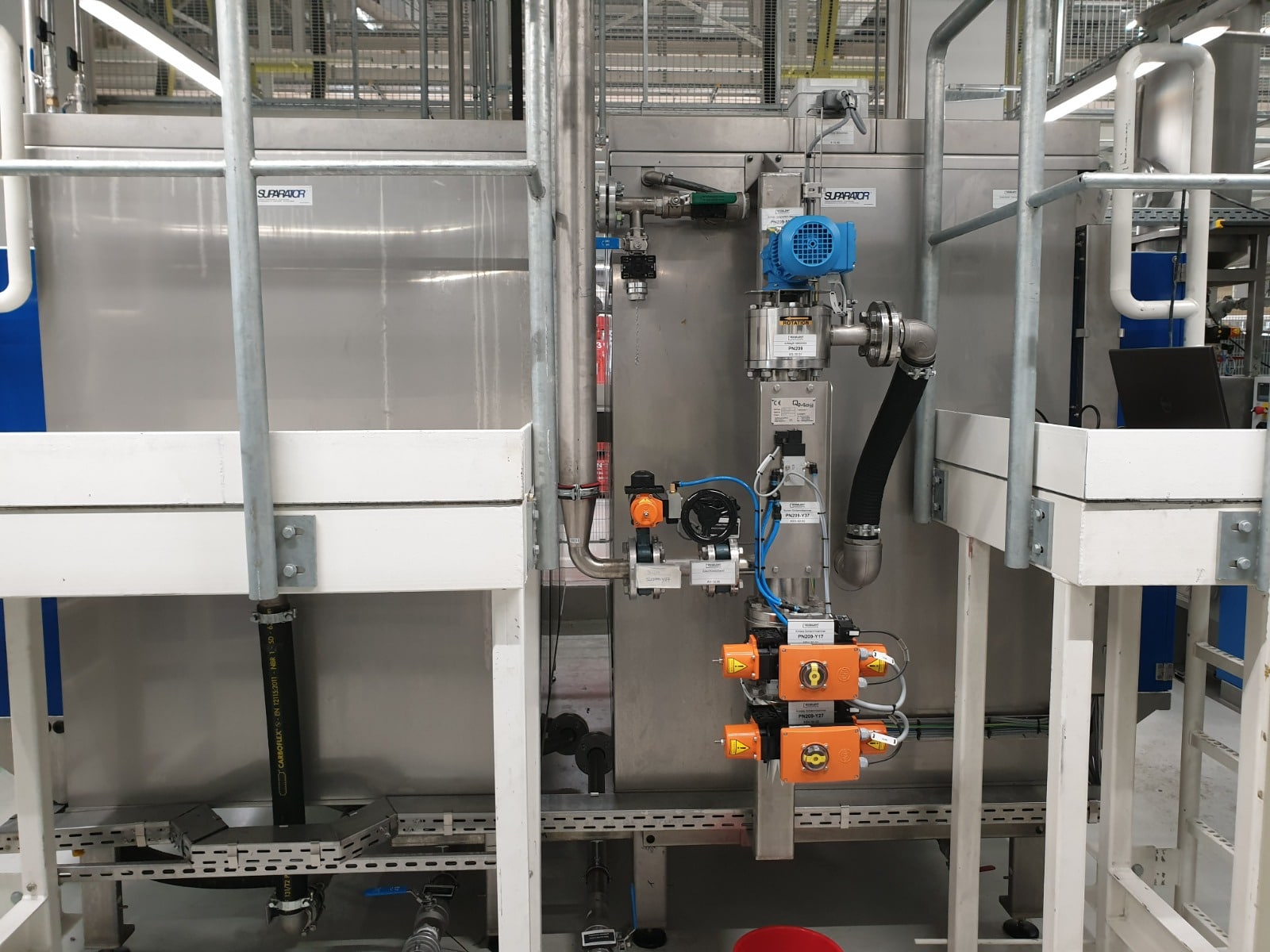
Application highlights
Particle filtration
Separating particles by means of filtration is clearly one of the most commonly used separation techniques. The metal industry frequently uses water or water based fluids in the production; plain water for high pressure de-burring, specialty cleaners or degreasers and complex emulsions for the machining. What all these applications have in common is that the water based medium gets polluted in the production process, which limits its life time.
Separating the pollution from the medium, during normal production, not only extends the life time but significantly adds to the product quality; pollution no longer affects the production process. If filtration can be done in an economical way, with minimal use of consumables and minimal waste being generated, an investment in the right filtrtion technology pays back very quickly.